Как рассчитать время закалки и отпуска
Опубликовано: 17.09.2024
Время нагрева деталей при отпуске берется из расчета 1 минута на 1 мм условной толщины (диаметр) детали.
Тогда время нагрева деталей при отпуске:
Время выдержки при высоком отпуске (выше 400 0 С) берется из расчета 10 минут + 1 минута на 1 мм условной толщины (диаметр) детали.
Тогда время выдержки деталей при отпуске:
Общее время отпуска определяется по формуле (1.1).
Тогда общее время при отпуске составит
Для выбора наиболее рациональных режимов высокочастотной закалки пользуются так называемыми номограммами преимущественных режимов. Номограмма представляет собой зависимость времени нагрева от диаметра нагреваемого изделия при определенной частоте тока.
Частота тока выбирается в зависимости от необходимой глубины закаленного слоя, которая определяется в соответствии с техническими требованиями детали. В данном дипломном проекте закалке токами высокой частоты подвергаются такие детали, как шток, вал, плунжер, ось. В соответствии с технологическими требованиями для этих деталей оптимальные свойства после закалки ТВЧ получаются при глубине закаленного слоя 1,5-2 мм, что соответствует использованию сравнительно высокой частоты в пределах 25000-440000 Гц. Условно зададимся средним значением частоты тока 66000 Гц.
Тогда время нагрева при закалке ТВЧ составит:
Охлаждение деталей проводится со скоростью , тогда оптимальное время для охлаждения детали с температуры нагрева 900 о С до температуры начала самоотпуска равной 200 о С составит 3 секунды.
Контроль технологических процессов термической обработки
Выполнение операций по контролю металлов и качества термической обработки сочетается с контролем за соблюдением технологических процессов.
Основным объектом контроля технологического процесса термической обработки являются контроль температуры, времени нагрева и выдержки, контроль атмосферы в печи, контроль глубины закаленного слоя, исправности индукторов, приспособлений и инструментов.
Вода для закалки и охлаждения электрооборудования установок должна отвечать требованиям по температуре, механическим и минеральным примесям.
При работе на установках с ламповым генератором контролируется анодное напряжение, напряжение на контуре, токи анода и сетки. А также контролируется скорость перемещения детали относительно индуктора и зазор между индуктором и деталью. Зазор контролируют индикатором, щупом или другим мерительным инструментом. Контроль скорости перемещения детали относительно индуктора выполняют при настройке режима для каждой партии.
Контроль атмосферы в рабочем пространстве печи проводят постоянно в процессе работы. Контроль приспособлений и инструмента осуществляют путем систематического осмотра внешнего вида и узлов крепления [8].
Основные виды брака и дефектов, возникающие при термической обработке
Под дефектом детали понимают каждое отклонение от формы, размеров, массы, внешнего вида, макро- и микроструктуры, физических или механических свойств и норм, установленных соответствующими стандартами или техническими условиями. Причины дефектов при термической обработке штоков следующие: применение сталей несоответствующих марок; внутренние пороки стали, своевременно не обнаруженные; нарушения технологического процесса термической обработки (температурного режима, состава среды, в которой происходит термообработка); применение неправильных приемов работы и контроля; неудачная конструкция детали
В процессе закалки при охлаждении стали в результате структурных превращений и изменения объема металла появляются внутренние напряжения. Эти напряжения приводят к следующим дефектам: образованию трещин, деформации и короблению, изменению объема стали, обезуглероживанию и окислению, появлению мягких пятен, низкой твердости и перегреву.
Закалочные трещины - это неисправимый брак, образующийся в процессе термической обработки. В крупных деталях, закалочные трещины могут появляться даже при закалке в масле. Поэтому такие детали целесообразно охлаждать до 150 - 200°С с быстрым последующим отпуском.
Трещины возникают при неправильном нагреве (перегреве), большой скорости охлаждения и при несоответствии химического состава стали.
Закалочные трещины возникают также при неправильной конструкции деталей, резких переходах, грубых рисках, оставшихся после механической обработки, острых углах, тонких стенках и т.д.
Закалочные трещины образуются чаще всего при слишком резком охлаждении или нагреве в результате возникающих в деталях внутренних напряжений. Это часто наблюдается при закалке легированных сталей. Поэтому детали из этих сталей нагревают медленнее, чем из углеродистых, и более равномерно крепления [8].
Закалочные трещины обычно располагаются в углах деталей и имеют дугообразный или извилистый вид.
В заводской практике часто встречаются поверхностные трещины, которые обычно располагаются в виде сплошной или разорванной сетки. Такие трещины возникают в процессе поверхностной закалки при нагреве токами высокой частоты или газопламенной закалки, когда охлаждение ведется слишком холодной водой, а также при перегреве металла.
Поверхностные трещины могут возникать не только в процессе термообработки, но и при шлифовании закаленных деталей, если они были неправильно отпущены.
Равномерный отпуск после закалки и правильные режимы шлифования полностью устраняют возникновение трещин.
Во избежание брака все участки (части) деталей, на которых обычно появляются трещины, обматывают асбестовым шнуром и замазывают огнеупорной глиной. Строгое выполнение технологических режимов закалки может сократить количество бракованных деталей до минимума.
Деформация и коробление деталей происходят в результате неравномерных структурных и связанных с ними объемных превращений и возникновения внутренних напряжений при охлаждении.
При закалке стали коробление во многих случаях происходит и без значительных объемных изменений, в результате неравномерного нагрева и охлаждения деталей. Если, например, деталь небольшого сечения и большой длины нагревать только с одной стороны, то она изгибается, нагретая сторона при этом удлиняется благодаря тепловому расширению и становится выпуклой, а противоположная - вогнутой. При одностороннем охлаждении в процессе закалки (особенно в воде) быстро охлажденная сторона детали за счет теплового сжатия станет вогнутой, а обратная сторона - выпуклой. Следовательно, нагревать и охлаждать детали при закалке следует равномерно. На деформацию особенно большое влияние оказывает способ охлаждения. Поэтому при погружении деталей и инструмента в закалочную среду надо учитывать их форму и размеры. Например детали, имеющие толстые и тонкие части, погружают в закалочную среду сначала толстой частью, длинные осевые детали (валы, штока, оси, сверла, метчики и другие) - в строго вертикальном положении, а тонкие плоские детали (диски, отрезные фрезы, пластинки и др.) - ребром.
Очень большое значение для уменьшения деформации и коробления деталей имеют правильно выбранные и изготовленные приспособления.
При массовом производстве для каждой детали изготовляются специальные приспособления. Стоимость их изготовления быстро окупается. При серийном производстве, когда обрабатываются большие партии разнообразных деталей, более экономично иметь универсальные приспособления.
Мягкие пятна - это участки на поверхности детали или инструмента с пониженной твердостью. Причинами такого дефекта могут быть наличие на поверхности деталей окалины и загрязнений, вызванных соприкосновением деталей друг с другом в процессе охлаждения в закалочной среде, участки с обезуглероженной поверхностью или недостаточно быстрое движение деталей в закалочной среде (паровая рубашка). Мягкие пятна полностью устраняются при струйчатой закалке и в подсоленной воде.
Перегрев при закалке вызывает крупнозернистую структуру с блестящим изломом и, следовательно, ухудшает механические свойства стали. Для измельчения зерна и подготовки структуры для повторной закалки перегретую сталь необходимо подвергать отжигу.
Недогрев получается в том случае, если температура закалки была ниже критической точки- для доэвтектоидных сталей и - для заэвтектоидных сталей.
При недогреве структура закаленной стали состоит из мартенсита и зерен феррита, который, как известно, имеет низкую твердость.
Виды брака при закалке ТВЧ следующие:
Продавливаниезакаленного слоя происходит в результате недостаточной его глубины.
Отколострых, не имеющих фасок кромок, в которых создаются повышенные напряжения.
Трещины возникающие из-за перегрева охлаждающей среды, недостатков в конструкции детали, острых кромок у отверстий и шпонок, шлицевых канавок и др.
Отслаивание закаленногослоя возникающий вследствие возникновения повышенных внутренних напряжений.
Контроль качества деталей
Контроль качества деталей осуществляют контролеры отдела технического контроля (ОТК).
Качество деталей, подвергаемых термической обработке, зависит от соблюдения режимов в соответствии с технологическим процессом производства деталей. Несоблюдение режимов нагрева, времени выдержки и охлаждения может привести к браку целой партии деталей.
Контроль за подготовкой деталей к термической обработке заключается в проверке чистоты деталей.
Сталь должна контролироваться на величину зерна (требуется не крупнее 5 номера) по ГОСТ 5639-82.
Глубина обезуглероженного слоя должна составлять менее 0,24 мм. Поверхностное обезуглероживание ухудшает прочность при статическом и многоцикловомнагружении и релаксационную стойкость, т.е. основные характеристики, определяющие долговечность штока, который работает в условиях больших угловых нагрузках в эксплуатации.
Методы контроля термической обработки должны соответствовать утвержденным инструкциям.
После термической обработки деталей проводят следующие контрольные операции, предусмотренные в инструкционных картах контроля:
1) Наружный осмотр деталей перед термической обработкой.
Наружный осмотр деталей проводят для определения внешних дефектов деталей (трещин, коробления). Для определения деформации прямолинейность деталей проверяют с помощью линейки. Внешние дефекты определяют с помощью 5 - 10-кратного увеличения или микроскопа. На поверхности штоков не допускаются трещины, риски, волосовины и другие грубые дефекты. Контроль размеров детали производят по свободной высоте, наружному или внутреннему диаметрам. В соответствии с техническими условиями, контролю подвергают 100% деталей от партии.
2) Испытание твёрдости деталей.
Твёрдость является одной из характеристик качества термической обработки. Твёрдость измеряется после закалки, высокого отпуска и ТВЧ. Контроль твёрдости проводится по методу Роквелла (ГОСТ 9013-59) на приборе ТК-2 путём вдавливания в зачищенную поверхность алмазного конуса при нагрузке Р = 1470 Н. Показания прибора снимают по шкале «С» - чёрного цвета [10].
3) Контроль деталей перед обработкой ТВЧ.
Детали должны поступать на поверхностную термическую обработку очищенными от масла, стружки и других загрязнений. На поверхностях, подлежащих закалке токами высокой частоты, не допускаются местные дефекты (риски, вмятины), глубина которых превышает припуск на последующую механическую обработку. Шероховатость поверхностей, подвергаемых закалке, должна быть не ниже 5-ого класса, RZ=20.
Все углы на деталях должны быть зачищены от заусенцев. При закалке цилиндрических и плоских поверхностей с отверстиями последние должны иметь фаски и для большой гарантии от образования трещин закрываться медными заглушками, влажным асбестом или медными трубками с деревянными пробками.
4) Проверка перпендикулярности опорных плоскостей деталей.
После закалки ТВЧ цилиндрических деталей обязательно проводят контроль перпендикулярности опорных плоскостей. Отклонение от перпендикулярности оси определяют в центрах или призмах с помощью индикатора часового типа (индикаторной головки). Отклонение от перпендикулярности допускается не более 0,3 мм.
5) Контроль микроструктуры.
Микроструктуру исследуют на микроскопах, вырезанных из и улучшенных образцов с помощью специальных шкал, разработанных для данной стали. Содержание углерода определяется послойным химическим или спектральным анализом.
Принятые контролером детали и инструмент клеймят кислотой, резиновым клеймом или окрашивают зеленой краской. На годные детали выписывают квитанцию за подписью работника ОТК, принявшего продукцию.
Бракованную продукцию после контроля окрашивают в желтый цвет и убирают в изолятор брака (металлический ящик) [10].
Тепловое воздействие на металл меняет его свойства и структуру. Это позволяет повысить механические свойства материала, долговечность и надежность изделий, а также уменьшить размеры и массу механизмов и машин. Кроме того, благодаря термообработке, для изготовления различных деталей можно применять более дешевые сплавы.
Как закалялась сталь
Термообработка стали заключается в тепловом воздействии на металл по определенным режимам ля изменения его структуры и свойств.
К операциям термообработки относятся:
- отжиг;
- нормализация;
- старение;
- закалка стали и отпуск стали (и пр.).
- температуры нагрева;
- времени (скорости) нагрева;
- продолжительности выдержки при заданной температуре;
- скорости охлаждения.
Закалка
При нагреве и охлаждении сталей происходит перестройка атомной решетки. Критические значения температур у разных марок сталей неодинаковы: они зависят от содержания углерода и легирующих примесей, а также от скорости нагрева и охлаждения.
После закалки сталь становится хрупкой и твердой. Поверхностный слой изделий при нагреве в термических печах покрывается окалиной и обезуглероживается тем более, чем выше температура нагрева и время выдержки в печи. Если детали имеют малый припуск для дальнейшей обработки, то брак этот является неисправимым. Режимы закалки закалки стали зависят от ее состава и технических требований к изделию.
Охлаждать детали при закалке следует быстро, чтобы аустенит не успел превратиться в структуры промежуточные (сорбит или троостит). Необходимая скорость охлаждения обеспечивается посредством выбора охлаждающей среды. При этом чрезмерно быстрое охлаждение приводит к появлению трещин или короблению изделия. Чтобы этого избежать, в интервале температур от 300 до 200 градусов скорость охлаждения надо замедлять, применяя для этого комбинированные методы закалки. Большое значение для уменьшения коробления изделия имеет способ погружения детали в охлаждающую среду.
Нагрев металла
Все способы закалки стали состоят из:
- нагрева стали;
- последующей выдержки для достижения сквозного прогрева изделия и завершения структурных превращений;
- охлаждения с определенной скоростью.
Изделия из углеродистой стали нагревают в камерных печах. Предварительный подогрев в этом случае не требуется, так как эти марки сталей не подвергаются растрескиванию или короблению.
Сложные изделия (например, инструмент, имеющий выступающие тонкие грани или резкие переходы) предварительно подогревают:
- в соляных ваннах путем двух-или трехкратного погружения на 2 – 4 секунды;
- в отдельных печах до температуры 400 – 500 градусов по Цельсию.
Нагрев всех частей изделия должен протекать равномерно. Если это невозможно обеспечить за один прием (крупные поковки), то делаются две выдержки для сквозного прогрева.
Если в печь помещается только одна деталь, то время нагрева сокращается. Так, например, одна дисковая фреза толщиной 24 мм нагревается в течение 13 минут, а десять таких изделий – в течение 18 минут.
Защита изделия от окалины и обезуглероживания
Для изделий, поверхности которых после термообработки не шлифуются, выгорание углерода и образование окалины недопустимо. Защищают поверхности от подобного брака применением защитных газов, подаваемых в полость электропечи. Разумеется, такой прием возможен только в специальных герметизированных печах. Источником подаваемого в зону нагрева газа служат генераторы защитного газа. Они могут работать на метане, аммиаке и других углеводородных газах.
Если защитная атмосфера отсутствует, то изделия перед нагревом упаковывают в тару и засыпают отработанным карбюризатором, чугунной стружкой (термисту следует знать, что древесный уголь не защищает инструментальные стали от обезуглероживания). Чтобы в тару не попадал воздух, ее обмазывают глиной.
Соляные ванны при нагреве не дают металлу окисляться, но от обезуглероживания не защищают. Поэтому на производстве их раскисляют не менее двух раз в смену бурой, кровяной солью или борной кислотой. Соляные ванны, работающие на температурах 760 – 1000 градусов Цельсия, весьма эффективно раскисляются древесным углем. Для этого стакан, имеющий множество отверстий по всей поверхности, наполняют просушенным углем древесным, закрывают крышкой (чтобы уголь не всплыл) и после подогрева опускают на дно соляной ванны. Сначала появляется значительное количество языков пламени, затем оно уменьшается. Если в течение смены таким способом трижды раскислять ванну, то нагреваемые изделия будут полностью защищены от обезуглероживания.
Степень раскисления соляных ванн проверяется очень просто: обычное лезвие, нагретое в ванне в течение 5 – 7 минут в качественно раскисленной ванне и закаленное в воде, будет ломаться, а не гнуться.
Охлаждающие жидкости
Основной охлаждающей жидкостью для стали является вода. Если в воду добавить небольшое количество солей или мыла, то скорость охлаждения изменится. Поэтому ни в коем случае нельзя использовать закалочный бак для посторонних целей (например, для мытья рук). Для достижения одинаковой твердости на закаленной поверхности необходимо поддерживать температуру охлаждающей жидкости 20 – 30 градусов. Не следует часто менять воду в баке. Совершенно недопустимо охлаждать изделие в проточной воде.
Недостатком водяной закалки является образование трещин и коробления. Поэтому таким методом закаливают изделия только несложной формы или цементированные.
- При закалке изделий сложной конфигурации из конструкционной стали применяется пятидесятипроцентный раствор соды каустической (холодный или подогретый до 50 – 60 градусов). Детали, нагретые в соляной ванне и закаленные в этом растворе, получаются светлыми. Нельзя допускать, чтобы температура раствора превышала 60 градусов.
Пары, образующиеся при закалке в растворе каустика, вредны для человека, поэтому закалочную ванну обязательно оборудуют вытяжной вентиляцией.
- Закалку легированной стали производят в минеральных маслах. Кстати, тонкие изделия из углеродистой стали также проводят в масле. Главное преимущество масляных ванн заключается в том, что скорость охлаждения не зависит от температуры масла: при температуре 20 градусов и 150 градусов изделие будет охлаждаться с одинаковой скоростью.
Следует остерегаться попадания воды в масляную ванну, так как это может привести к растрескиванию изделия. Что интересно: в масле, разогретом до температуры выше 100 градусов, попадание воды не приводит к появлению трещин в металле.
Недостатком масляной ванны является:
- выделение вредных газов при закалке;
- образование налета на изделии;
- склонность масла к воспламеняемости;
- постепенное ухудшение закаливающей способности.
- Стали с устойчивым аустенитом (например, Х12М) можно охлаждать воздухом, который подают компрессором или вентилятором. При этом важно не допускать попадания в воздухопровод воды: это может привести к образованию трещин на изделии.
- Ступенчатая закалка выполняется в горячем масле, расплавленных щелочах, солях легкоплавких.
- Прерывистая закалка сталей в двух охлаждающих средах применяется для обработки сложных деталей, изготовленных из углеродистых сталей. Сначала их охлаждают в воде до температуры 250 – 200 градусов, а затем в масле. Изделие выдерживается в воде не более 1 – 2 секунд на каждые 5 – 6 мм толщины. Если время выдержки в воде увеличить, то на изделии неизбежно появятся трещины. Перенос детали из воды в масло следует выполнять очень быстро.
Вам нужно быстро и качественно нарезать металл? Воспользуйтесь плазменной резкой! Как правильно ее выполнять, читайте в этой статье.
Если вас интересует, как сделать токарную обработку металлических изделий, читайте статью по https://elsvarkin.ru/obrabotka-metalla/tokarnaya-obrabotka-metalla-obshhie-svedeniya/ ссылке.
Процесс отпуска
Отпуску подвергаются все закаленные детали. Это делается для снятия внутренних напряжений. В результате отпуска несколько снижается твердость и повышается пластичность стали.
В зависимости от требуемой температуры отпуск производится :
- в масляных ваннах;
- в селитровых ваннах;
- в печах с принудительной воздушной циркуляцией;
- в ваннах с расплавленной щелочью.
Температура отпуска зависит от марки стали и требуемой твердости изделия, например, инструмент, для которого необходима твердость HRC 59 – 60, следует отпускать при температуре 150 – 200 градусов. В этом случае внутренние напряжения уменьшаются, а твердость снижается незначительно.
Быстрорежущая сталь отпускается при температуре 540 – 580 градусов. Такой отпуск называют вторичным отвердением, так как в результате твердость изделия повышается.
Изделия можно отпускать на цвет побежалости, нагревая их на электроплитах, в печах, даже в горячем песке. Окисная пленка, которая появляется в результате нагрева, приобретает различные цвета побежалости, зависящие от температуры. Прежде чем приступать к отпуску на один из цветов побежалости, надо очистить поверхность изделия от окалины, нагара масла и т. д.
Обычно после отпуска металл охлаждают на воздухе. Но хромоникелевые стали следует охлаждать в воде или масле, так как медленное охлаждение этих марок приводит к отпускной хрупкости.
пуска на различные температуры позволяет получить представление об изменении структуры после различных режимов закалки и отпуска.
Методика расчета результатов закалки и отпуска заключается в следующем.
Для расчета необходимы следующие исходные данные:
1. Распределение скоростей охлаждения по сечению изделия (определяется, как указано в первом разделе данной главы), подвергаемого термической обработке.
2. Кривая изменения твердости вдоль торцового образца после стандартного испытания или термокинетическая диаграмма для стали данной плавки или марки.
3. Кривые изменения твердости вдоль торцового образца после стандартного испытания и последующего отпуска при различных температурах, аналогичных показанным на рис. 194.
Практически все необходимые данные, кроме относящихся к изделию, могут быть получены на 1—2 образцах для торцовой пробы путем измерения твердости вдоль образующей, непосредственно после стандартного испытания на прокаливаемость и последующего отпуска при температурах 100, 200, 300° и т. д.
Имея эти сведения, можно рассчитать распределение твердости по сечению цилиндрического изделия.
Для примера проведем этот расчет для изделия из стали 40Х после закалки в масле в отпуске при 600°.
1. Исходные данные показаны на рис. 184 и 185.
Состав стали: 0,44% С и 1,04% Сг. Температура нагрева под
закалку и в условиях проведения торцовой пробы на прокаливаемость равна 840°.
2. По кривой рис. 182 определяем скорости охлаждения через каждые 10 мм (от сердцевины).
3. По градуировочной кривой для образца торцовой пробы на прокаливаемость (см. рис. 171) определяем расстояния от торца, соответствующие указанным скоростям охлаждения.
4. По вычисленным расстояниям от торца х и кривой прокаливаемости для стали 40Х (рис. 185) определяем твердости, соответствующие величинам х, т. е. заданной скорости охлаждения.
5. Зная соответствие между х, мм, и расстоянием от сердцевины цилиндра, составляем таблицу распределения твердости по сечению цилиндра после закалки в масле.
6. По известному расстоянию от торца и кривой твердости для отпуска 600° (рис. 185) определяем твердость после полного цикла термической обработки.
7. По этим результатам строим кривые распределения твердости после закалки в масле и отпуска при 600° (кривые 1 и 2 рис. 186, соответственно).
Описанный метод может быть использован не только для закалки, но и для отжига и нормализации.
В том случае, когда закон распределения скоростей охлаждения по сечению неизвестен и изделие имеет достаточно простую форму, расчет можно провести по методике, описанной в разделе 2 настоящей главы (по величине характеристического расстояния).
Зная распределение твердости по сечению после закалки и используя кривые рис. 185, можно определить твердости при любой температуре отпуска. Для этой цели из точки 1 на кривой для образца без отпуска нужно опустить перпендикуляр до пересечения с кривой твердости для данной температуры отпуска (см. рис. 185). В точке пересечения (в данном случае в точке 2
для отпуска при 650°) получаем: твердость понизилась от 40 до 21 HRC. Повторяя эту операцию для нескольких точек по сечению закаленного тела, узнаем распределение твердости по сечению после отпуска при 650°.
Применяя эту методику расчета, практически можно рассчитать результаты основных процессов термической обработки стали: закалки, отпуска, отжига и нормализации.
Практические расчеты значительно сокращают время экспериментирования и позволяют правильно выбирать материал и технологические режимы.
Автор: Администрация
_ _ _ _ _ _ _ _ _ _ _ _ _ _ _ _ _ _ _ _ _ _ _ _ _ _ _ _ _ _ _ _ _ _ _ _ _ _ _ _ _ _ _ _ _ _ _ _ _ _ _ _ _ _ _ _ _ _ _ _ _ _ _ _ _ _ _ _ _ _ _ _ _ _ _ _ _ _ _ _ _ _ _ _ _ _ _ _ _ _ _ _ _ _ _ _ _ _ _ _ _ _ _ _ _ _ _ _ _ _ _ _ _ _ _ _ _ _ _ _ _ _ _ _ _ _ _ _ _ _ _ _ _ _ _ _ _ _ _ _ _ _ _ _ _ _ _ _ _ _ _ _ _ _ _ _ _ _ _ _ _ _ _ _ _ _ _ _ _ _ _ _ _ _ _ _ _ _ _ _ _ _ _ _ _ _ _ _ _ _ _ _ _ _ _ _ _ _ _ _ _ _ _ _ _ _ _ _ _ _ _ _ _ _ _ _ _ _ _ _ _ _ _ _ _ _ _ _ _ _ _ _ _ _ _ _ _ _ _ _ _ _ _ _ _ _ _ _ _ _ _ _ _ _ _ _ _ _ _ _ _ _ _ _ _ _ _ _ _ _ _ _ _ _ _ _ _ _ _
Закалка. Стали с содержанием углерода меньше 0,25% в результате закалки свои свойства изменяют незначительно, поэтому обычно их не закаливают. Закалку применяют для увеличения твердости, прочности и износостойкости деталей, получаемых из поковок. В практике обычно закаливают рабочие части различного технологического инструмента, измерительного инструмента, тяжелонагруженные и работающие на истирание детали машин.Нагрев стали под закалку осуществляют в горнах или нагревательных печах. Детали в горны укладывают так, чтобы холодное дутье воздуха не попадало непосредственно на сталь. Нужно следить, чтобы нагрев происходил равномерно. Чем больше углерода и легирующих элементов содержит сталь, чем массивнее деталь и сложнее ее форма, тем медленнее должна быть скорость нагрева под закалку. Продолжительность выдержки при закалочной температуре ориентировочно принимается равной 0,2 от времени нагрева. Слишком длительная выдержка при закалочной температуре не рекомендуется, так как при этом интенсивно растут зерна и сталь теряет прочность. Охлаждение является исключительно важной операцией закалки, так как от него практически зависит получение требуемой структуры в металле. Для этого должно быть достаточное количество охлаждающей жидкости, чтобы температура во время нахождения в ней детали повышалась незначительно. Для достижения равномерной закалки нагретую деталь надо быстро погрузить в охлаждающую жидкость и перемешать ее в жидкости до полного охлаждения. Если закаливают только конец или часть изделия (например лезвие топора), те его опускают в закалочную жидкость на требуемую глубину и перемещают вверхвниз, так чтобы не было резкой границы скорости остывания между закаливаемой и незакаливаемой частями изделия и не появились трещины в переходной части.
Выбор охлаждающей среды зависит от марки стали, величины сечения детали и требуемых свойств, которые должна получить сталь после закалки. Стали с содержанием углерода от 0,3 до 0,6% обычно охлаждают в воде, а с большим содержанием углерода - в масле. При этом следует учитывать конфигурацию деталей и их сечение. Детали со сложной конфигурацией, с резкими переходами от малого сечения к большому и массивные детали охлаждать в воде опасно, так как на них могут появиться трещины. При определенном навыке можно применять следующий режим охлаждения. На несколько секунд погрузить деталь в воду, а затем быстро перенести ее в масло. Ориентировочное время охлаждения в воде до переноса в масло составляет 1. 1,5 с на каждые 5. 6 мм сечения детали. Такой способ охлаждения получил название «через воду в масло» или прерывистой закалки.» Ее применяют для закалки инструмента из углеродистой стали.При большом сечении детали наружные слои охлаждаются быстрее, чем внутренние, и поэтому твердость на поверхности получается больше, чем в середине. Углеродистые стали, например стали 40 и 45, закаливаются на глубину 4. 5 мм, а глубже будут частично закаленная зона и незакаленная сердцевина. Легирующие элементы — марганец, хром, никель и др. способствуют более глубокой закалке. Например, сталь 30Х закаливается на глубину 6. 9 мм, сталь 40СХ - на глубину 12 мм и сталь ЗОХНЗ - на глубину 10 мм.Некоторые детали нуждаются в большои прочности на поверхности при сохранении мягкой и вязкой сердцевины. Такие детали рекомендуется подвергать поверхностной закалке. Один из самых простых способов такой закалки состоит в загрузке детали в печь с высокой температурой (950. 1000 °С), быстром нагреве поверхности до закалочной температуры и охлаждении с большой скоростью в проточной охлаждающей среде.Часто закалку выполняют сразу после ковки без дополнительного нагрева, если температура поковки после ковки будет не ниже закалочной температуры.Закалка может быть сильной, умеренной и слабой. Для получениясильной закалки в качестве охлаждающей среды применяют воду при 15. 20°С до погружения в нее детали и водные растворы поваренной соли и соды (карбоната натрия). Умеренная закалка получается при использовании воды со слоем масла толщиной 20. 40 мм, нефти, мазута, мыльной воды, жидкого минерального масла, а также горячей воды. Слабая закалка получается, если применять в качестве охлаждающей среды струю воздуха или расплавленный свинец и его сплавы. Закалка требует внимания и умения. Плохая закалка может испортить почти готовые детали, т. е. привести к образованию трещин, перегреву и обезуглероживание поверхности, а также к желоблению (короблению), которое в значительной степени зависит от способа и скорости погружения детали в охлаждающую жидкость.Закалка - не окончательная операция термической обработки, так как после ее сталь становится не только прочной и твердой, но и очень хрупкой, а в поковке возникают большие закалочные напряжения. Эти напряжения достигают таких значений, при которых в поковках появляются трещины или детали из этих поковок разрушаются в самом начале их эксплуатации. Например, только что закаленный кузнечный молоток нельзя использовать, так как при ударах им о металл от него будут откалываться кусочки металла. Поэтому для уменьшения хрупкости, внутренних закалочных напряжений и получения требуемых прочностных свойств стали после закалки поковки подвергают отпуску. Отпуск состоит в нагревании закаленной стали до температуры ниже Ас1 (см. рисунок), выдержке при этой температуре некоторое время и быстрого или медленного охлаждения, как правило, на воздухе. В процессе отпуска в металле структурных изменений не происходит, однако уменьшаются закалочные напряжения, твердость и прочность, а пластичность и вязкость увеличиваются. В зависимости от марки стали и от предъявляемых к детали требований по твердости, прочности и пластичности применяют следующие виды отпусков1. Высокий отпуск состоит в нагреве закаленной детали до температуры 450. 650°С, выдержке при этой температуре и охлаждении. Углеродистые стали охлаждаются на воздухе, а хромистые, марганцовистые, хромокремниевые - в воде, так как медленное охлаждение их приводит к отпускной хрупкости. При таком отпуске почти полностью ликвидируются закалочные напряжения, увеличивается пластичность и вязкость, хотя заметно уменьшается твердость и прочность стали. Закалка с высоким отпуском по сравнению с отжигом, создает наилучшее соотношение между прочностью стали и ее вязкостью. Такое сочетание термообработки называют улучшением Улучшению подвергают сильнонагруженные детали машии, изготовленные из углеродистых сталей с содержанием углерода 0,3. 0,5%.2. Средний отпуск состоит в нагреве закаленной детали до температуры 300. 450°С, выдержке при этой температуре и охлаждении на воздухе. При таком отпуске увеличивается вязкость стали и снимаются внутренние напряжения в ней при сохранении достаточно большой твердости. Он применяется для деталей машин, работающих в условиях трения и динамических нагружеиий.3. Низкий отпуск состоит в нагреве закалении детали до температуры 140. 250 °С и охлаждении с любой скоростью. При таком отпуске почти не уменьшается твердость и вязкость стали, но зато снимаются внутренние закалочные напряжения. После такого отпуска детали нельзя нагружать динамическими нагрузками. Чаще всего его используют для обработки режущего и измерительного инструмента из углеродистых и легированных сталей.При изготовлении слесарного, кузнечного или измерительного инструмента ручной ковкой кузнецы часто применяют закалку и отпуск с одного нагрева. Такую операцию называют самоотпуском и выполняют следующим образом. Нагретую под закалку поковку охлаждают в воде или масле не полностью, а до температуры несколько выше температуры отпуска, которую можно определить при извлечении поковки из закалочной среды, по цвету побежалости на предварительно обработанной на наждачном круге поверхности поковки. После этого поковку окончательно охлаждают путем погружения ее в воду или масло.
Закалка. Это процесс термической обработки, при которой сталь нагревают до оптимальной температуры, выдерживают при этой температуре и затем быстро охлаждают с целью получения неравновесной структуры. В результате закалки повышается прочность и твердость и понижается пластичность конструкционных и инструментальных сталей и сплавов. Качество закалки зависит от температуры и скорости нагрева, времени выдержки и охлаждения. Основными параметрами закалки являются температура нагрева и скорость охлаждения.
Температуру нагрева для закалки определяют по положению критических точек Ac1 и Ас3. Доэвтектоидные углеродистые стали при закалке нагревают на 30-50°С выше верхней критической точки Ас3, а заэвтектоидные - на 30-50°С выше точки Ас1 (рис. 41).
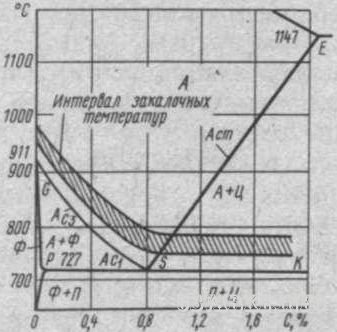
Рис. 41. Интервалы температур нагрева стали при закалке
Скорость нагрева и время выдержки зависят от химического состава стали, размеров, массы и конфигурации закаливаемых деталей, типа нагревательных печей и нагревательной среды. Чем больше размеры и сложнее конфигурация закаливаемых деталей, тем медленнее происходит нагрев. Детали из высокоуглеродистых и легированных сталей, имеющих пониженную теплопроводность, нагревают медленно и с более длительной выдержкой при нагреве по сравнению с деталями из низкоуглеродистых сталей. Это делается для того, чтобы уменьшить деформацию деталей при нагреве.
Скорость нагрева и продолжительность выдержки определяют экспериментально или по технологическим картам, в которых указывают температуру, время нагрева для каждого вида деталей или инструмента. Ориентировочно время нагрева в электрических печах принимают 1,5-2 мин на 1 мм сечения изделия.
Оборудованием для нагрева стали служат нагревательные термические печи и печи-ванны, которые подразделяют на электрические и топливные, обогреваемые за счет сгорания топлива (газа, мазута, угля и др.).
Средой, в которой нагревают сталь, являются в печах - газовая среда (воздух, продукты сгорания топлива), нейтральный газ; в печах-ваннах - минеральные масла, расплавленные соли и металлы.
При нагреве в электрических печах в среде атмосферного воздуха, а также в печах с газовой средой сталь, взаимодействуя со средой, окисляется и на ее поверхности образуется окалина. Кроме того, происходит обезуглероживание - частичное выгорание углерода в поверхностных слоях стали, что снижает прочностные свойства материала после закалки. Наиболее благоприятен нагрев в печах с нейтральной или защитной атмосферой, обеспечивающей предохранение деталей от окисления.
Нагрев стали до требуемой температуры и выдерживание при этой температуре необходимо проводить как можно быстрее. Чем меньше сталь будет находиться в условиях высоких температур, тем выше ее свойства после закалки. Однако время нагрева должно быть достаточным, чтобы сталь равномерно прогревалась по всему объему и получила аустенитную структуру. Поэтому наиболее эффективным по скорости нагрева и предупреждению окисления стали является нагрев в печах-ваннах, наполненных расплавленным металлом (свинец) или расплавленными солями: NaOH, ВаСl2 или 50% КСl+50% NaC03. Нагрев в печах-ваннах с использованием расплавленного металла или солей происходит в 4-5 раз быстрее, чем в печах с газовой средой.
В качестве закалочных сред используют воду, водные растворы солей, щелочей, масло и расплавленные соли, имеющие различную охлаждающую способность. Если принять охлаждающую способность воды при 20°С за единицу, то охлаждающая способность масла будет равна 0,17-0,44, расплавленного свинца (при 335°С) - 0,05, воздуха - 0,03. При нагреве воды с 20 до 99°С охлаждающая способность ее изменяется от 1 до 0,07. В зоне перлитных превращений (650°С) вода охлаждает в 5-6 раз быстрее, чем масло. Воду применяют в основном для охлаждения углеродистых сталей. В масле охлаждают легированные стали.
Закалочные среды (вода, масло) действуют следующим образом. На первом этапе, в момент погружения изделия в закалочную среду, вокруг изделия образуется пленка перегретого пара (паровая рубашка). Через слой паровой рубашки охлаждение изделия происходит относительно медленно. Это этап пленочного кипения. Затем паровая рубашка разрывается и охлаждающая жидкость начинает кипеть на поверхности изделия. Это этап пузырчатого кипения. На этом втором этапе охлаждение изделия происходит быстро. Когда температура поверхности изделия станет ниже температуры кипения жидкости, жидкость не кипит и охлаждение изделия замедлится. Это третий этап - этап конвективного теплообмена. Чем шире интервал этапа пузырчатого кипения, тем интенсивнее охлаждает сталь закалочная жидкость.
Закалка в одной среде – наиболее простой и распространенный способ (рис. 42, кривая а). Деталь или инструмент, нагретые до температуры закалки, погружают в закалочную жидкость (вода, масло и т. д.), в которой она находится до полного охлаждения.
Этот способ используют при ручной и механизированной закалке, когда детали автоматически поступают из печи после нагрева в закалочную жидкость, в воду или масло. Недостатком этого способа закалки является то. что деталь охлаждается по сечению неравномерно и в ней возникают большие термические напряжения.
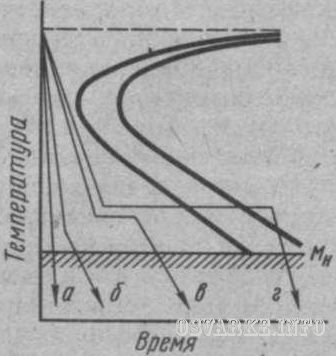
Рис. 42. Схема различных способов закалки:
а - закалка в одной среде, б - закалка в двух средах, в - ступенчатая закалка, г - изотермическая закалка
При закалке в двух средах, или прерывистой закалке (рис. 42, кривая б), деталь, нагретую до заданной температуры, сначала погружают в быстро охлаждающую среду - воду, а затем переносят деталь в медленно охлаждающую среду - масло. Такую закалку применяют для обработки инструмента, изготовленного из высокоуглеродистой стали. При этом способе закалки трудно определить точное время пребывания детали в каждой из сред.
Ступенчатая закалка (рис. 42, кривая в) заключается в том, что нагретые детали сначала охлаждают до температуры несколько выше мартенситной точки Мн в горячем масле или расплавленной соли, а затем после короткой изотермической выдержки, необходимой для выравнивания температуры по всему сечению изделия, охлаждают на воздухе. Длительность изотермической выдержки по времени должна быть меньше времени устойчивости аустенита при этой температуре. На второй стадии охлаждения сталь закаливается. При таком виде закалки уменьшаются термические напряжения, коробление и предотвращается образование трещин.
Изотермическая закалка (рис. 42, кривая г) выполняется так же, как и ступенчатая, но выдержка в закалочной среде более продолжительная. При такой выдержке происходит изотермический распад аустенита с образованием бейнита. В качестве закалочной среды используют расплавленные соли или щелочи (20% NaOH и 80% КОН) с добавками 5-10% воды для увеличения скорости охлаждения. Изотермической закалке подвергают детали и инструмент из легированных сталей марок 6ХС, 9ХС, ХВГ и др.
Закалку с подстуживанием применяют для уменьшения разницы в температурах металла и закалочной среды, если деталь нагрета до температуры, значительно превышающей температуру закалки данной стали. Нагретую деталь перед погружением в закалочную среду выдерживают (подстуживают) на спокойном воздухе. Этот способ закалки обеспечивает уменьшение внутренних напряжений и предотвращает коробление деталей, особенно деталей, подвергнутых цементации
Закалка с самоотпуском состоит в том, что нагретую деталь . рабочей частью погружают в закалочную среду и выдерживают в ней не до полного охлаждения. За счет тепла нерабочей части детали, которая не погружалась в закалочную жидкость, рабочая часть детали или инструмента нагревается. Температуру отпуска при этом способе закалки определяют по цветам побежалости, возникающим на поверхности детали при температурах 220-300°С.
Закалку с самоотпуском применяют для обработки зубил, кернеров, бородков и других ударных инструментов, у которых твердость должна плавно понижаться от рабочей части к нерабочей.
Закалка с обработкой холодом заключается в продолжении охлаждения закаленной стали до температур ниже комнатной, но в интервале начала (Мн) и окончания (Мк) мартенситного превращения (см. рис. 38), для дополнительного более полного превращения остаточного аустенита в мартенсит и повышения твердости. Высокоуглеродистые и легированные стали после закалки при комнатной температуре содержат до 12% остаточного аустенита, а быстрорежущие - более.35%. В результате обработки холодом повышается твердость и стабилизируются размеры деталей. Наиболее распространенной охлаждающей средой служит смесь ацетона и твердой углекислоты (-78°С).
Закаливаемость - это способность стали приобретать максимально высокую твердость после закалки. Закаливаемость зависит главным образом от содержания углерода в стали: чем больше углерода, тем выше твердость. Это объясняется тем, что с повышением содержания углерода увеличивается число атомов углерода, удерживаемых в атомной решетке железа при закалке, т. е. увеличивается степень пересыщения твердого раствора углерода в железе.
Углеродистые стали с содержанием углерода менее 0,3% (сталь 20, СтЗ) не способны принимать закалку, так как не происходит образования мартенситной структуры. Образование мартенситной структуры связано с перестройкой атомной решетки железа из гранецентрированной в объемно-центрированную. Температура, при которой происходит такая перестройка, зависит от содержания углерода (см. рис. 38). Чем больше содержание углерода, тем ниже температура образования мартенситной структуры.
При выборе охлаждающей среды для того или иного способа закалки необходимо учитывать закаливаемость и прокаливаемость данной стали.
Прокаливаемость - это глубина проникновения закаленной зоны, т. е. способность стали закаливаться на определенную глубину. За глубину закаленной зоны принимают расстояние от поверхности до слоя, где в структуре будет примерно одинаковое количество мартенсита и троостита. Прокаливаемость зависит от химического состава стали, размеров деталей и условий охлаждения. С увеличением содержания углерода до 0,8% прокаливаемость стали увеличивается. При дальнейшем увеличении углерода прокаливаемость несколько снижается. Увеличению прокаливаемости также способствует укрупнение зерен аустенита при нагреве под закалку. Нерастворимые частицы, неоднородность аустенита и другие факторы, которые уменьшают устойчивость переохлажденного аустенита, уменьшают прокаливаемость. Все легирующие элементы, за исключением кобальта, увеличивают прокаливаемость. При комплексном легировании полезное влияние отдельных элементов на прокаливаемость взаимно усиливается.
При закалке скорость охлаждения по сечению изделия распределяется неравномерно. У поверхности она максимальная, в центре - минимальная, т. е. скорость охлаждения уменьшается по некоторому закону от поверхности изделия к его центру. Характеристикой прокаливаемости является критический диаметр, т. е. диаметр максимального сечения, которое прокаливается полностью в данной охлаждающей среде.
Отпуск - процесс термической обработки, состоящий в нагреве закаленной стали до температуры ниже критической точки Ас1), выдержке при этой температуре и последующем охлаждении (обычно на воздухе). Цель отпуска - получение более устойчивого структурного состояния, устранение или уменьшение напряжений, повышение вязкости и пластичности, а также понижение твердости и уменьшение хрупкости закаленной стали (рис. 43). Правильное выполнение отпуска в значительной степени определяет качество закаленной детали. Температура отпуска варьируется в широких пределах - от 150 до 700°С в зависимости от его цели. Различают низкий, средний и высокий отпуск.
Низкий отпуск характеризуется нагревом в интервале 150-250°С, выдержкой при этой температуре и последующим охлаждением на воздухе. Он выполняется с целью получения структуры мартенсита отпуска и для частичного снятия внутренних напряжений в закаленной стали с целью повышения вязкости без заметного снижения твердости. Низкий отпуск применяют для инструментальных сталей, после цементации и т. д.
Средний отпуск производится при температурах 300-500°С для получения структуры троостита отпуска. Твердость сталей заметно понижается, вязкость увеличивается. Этот отпуск применяют для пружин, рессор, а также инструмента, который должен иметь значительную прочность и упругость при достаточной вязкости.

Рис. 43. Влияние температуры отпуска на механичесуие свойства стали 40
Читайте также: