Какие печи применяются для закалки и высокого отпуска труб
Опубликовано: 11.05.2024
Тепловое воздействие на металл меняет его свойства и структуру. Это позволяет повысить механические свойства материала, долговечность и надежность изделий, а также уменьшить размеры и массу механизмов и машин. Кроме того, благодаря термообработке, для изготовления различных деталей можно применять более дешевые сплавы.
Как закалялась сталь
Термообработка стали заключается в тепловом воздействии на металл по определенным режимам ля изменения его структуры и свойств.
К операциям термообработки относятся:
- отжиг;
- нормализация;
- старение;
- закалка стали и отпуск стали (и пр.).
- температуры нагрева;
- времени (скорости) нагрева;
- продолжительности выдержки при заданной температуре;
- скорости охлаждения.
Закалка
При нагреве и охлаждении сталей происходит перестройка атомной решетки. Критические значения температур у разных марок сталей неодинаковы: они зависят от содержания углерода и легирующих примесей, а также от скорости нагрева и охлаждения.
После закалки сталь становится хрупкой и твердой. Поверхностный слой изделий при нагреве в термических печах покрывается окалиной и обезуглероживается тем более, чем выше температура нагрева и время выдержки в печи. Если детали имеют малый припуск для дальнейшей обработки, то брак этот является неисправимым. Режимы закалки закалки стали зависят от ее состава и технических требований к изделию.
Охлаждать детали при закалке следует быстро, чтобы аустенит не успел превратиться в структуры промежуточные (сорбит или троостит). Необходимая скорость охлаждения обеспечивается посредством выбора охлаждающей среды. При этом чрезмерно быстрое охлаждение приводит к появлению трещин или короблению изделия. Чтобы этого избежать, в интервале температур от 300 до 200 градусов скорость охлаждения надо замедлять, применяя для этого комбинированные методы закалки. Большое значение для уменьшения коробления изделия имеет способ погружения детали в охлаждающую среду.
Нагрев металла
Все способы закалки стали состоят из:
- нагрева стали;
- последующей выдержки для достижения сквозного прогрева изделия и завершения структурных превращений;
- охлаждения с определенной скоростью.
Изделия из углеродистой стали нагревают в камерных печах. Предварительный подогрев в этом случае не требуется, так как эти марки сталей не подвергаются растрескиванию или короблению.
Сложные изделия (например, инструмент, имеющий выступающие тонкие грани или резкие переходы) предварительно подогревают:
- в соляных ваннах путем двух-или трехкратного погружения на 2 – 4 секунды;
- в отдельных печах до температуры 400 – 500 градусов по Цельсию.
Нагрев всех частей изделия должен протекать равномерно. Если это невозможно обеспечить за один прием (крупные поковки), то делаются две выдержки для сквозного прогрева.
Если в печь помещается только одна деталь, то время нагрева сокращается. Так, например, одна дисковая фреза толщиной 24 мм нагревается в течение 13 минут, а десять таких изделий – в течение 18 минут.
Защита изделия от окалины и обезуглероживания
Для изделий, поверхности которых после термообработки не шлифуются, выгорание углерода и образование окалины недопустимо. Защищают поверхности от подобного брака применением защитных газов, подаваемых в полость электропечи. Разумеется, такой прием возможен только в специальных герметизированных печах. Источником подаваемого в зону нагрева газа служат генераторы защитного газа. Они могут работать на метане, аммиаке и других углеводородных газах.
Если защитная атмосфера отсутствует, то изделия перед нагревом упаковывают в тару и засыпают отработанным карбюризатором, чугунной стружкой (термисту следует знать, что древесный уголь не защищает инструментальные стали от обезуглероживания). Чтобы в тару не попадал воздух, ее обмазывают глиной.
Соляные ванны при нагреве не дают металлу окисляться, но от обезуглероживания не защищают. Поэтому на производстве их раскисляют не менее двух раз в смену бурой, кровяной солью или борной кислотой. Соляные ванны, работающие на температурах 760 – 1000 градусов Цельсия, весьма эффективно раскисляются древесным углем. Для этого стакан, имеющий множество отверстий по всей поверхности, наполняют просушенным углем древесным, закрывают крышкой (чтобы уголь не всплыл) и после подогрева опускают на дно соляной ванны. Сначала появляется значительное количество языков пламени, затем оно уменьшается. Если в течение смены таким способом трижды раскислять ванну, то нагреваемые изделия будут полностью защищены от обезуглероживания.
Степень раскисления соляных ванн проверяется очень просто: обычное лезвие, нагретое в ванне в течение 5 – 7 минут в качественно раскисленной ванне и закаленное в воде, будет ломаться, а не гнуться.
Охлаждающие жидкости
Основной охлаждающей жидкостью для стали является вода. Если в воду добавить небольшое количество солей или мыла, то скорость охлаждения изменится. Поэтому ни в коем случае нельзя использовать закалочный бак для посторонних целей (например, для мытья рук). Для достижения одинаковой твердости на закаленной поверхности необходимо поддерживать температуру охлаждающей жидкости 20 – 30 градусов. Не следует часто менять воду в баке. Совершенно недопустимо охлаждать изделие в проточной воде.
Недостатком водяной закалки является образование трещин и коробления. Поэтому таким методом закаливают изделия только несложной формы или цементированные.
- При закалке изделий сложной конфигурации из конструкционной стали применяется пятидесятипроцентный раствор соды каустической (холодный или подогретый до 50 – 60 градусов). Детали, нагретые в соляной ванне и закаленные в этом растворе, получаются светлыми. Нельзя допускать, чтобы температура раствора превышала 60 градусов.
Пары, образующиеся при закалке в растворе каустика, вредны для человека, поэтому закалочную ванну обязательно оборудуют вытяжной вентиляцией.
- Закалку легированной стали производят в минеральных маслах. Кстати, тонкие изделия из углеродистой стали также проводят в масле. Главное преимущество масляных ванн заключается в том, что скорость охлаждения не зависит от температуры масла: при температуре 20 градусов и 150 градусов изделие будет охлаждаться с одинаковой скоростью.
Следует остерегаться попадания воды в масляную ванну, так как это может привести к растрескиванию изделия. Что интересно: в масле, разогретом до температуры выше 100 градусов, попадание воды не приводит к появлению трещин в металле.
Недостатком масляной ванны является:
- выделение вредных газов при закалке;
- образование налета на изделии;
- склонность масла к воспламеняемости;
- постепенное ухудшение закаливающей способности.
- Стали с устойчивым аустенитом (например, Х12М) можно охлаждать воздухом, который подают компрессором или вентилятором. При этом важно не допускать попадания в воздухопровод воды: это может привести к образованию трещин на изделии.
- Ступенчатая закалка выполняется в горячем масле, расплавленных щелочах, солях легкоплавких.
- Прерывистая закалка сталей в двух охлаждающих средах применяется для обработки сложных деталей, изготовленных из углеродистых сталей. Сначала их охлаждают в воде до температуры 250 – 200 градусов, а затем в масле. Изделие выдерживается в воде не более 1 – 2 секунд на каждые 5 – 6 мм толщины. Если время выдержки в воде увеличить, то на изделии неизбежно появятся трещины. Перенос детали из воды в масло следует выполнять очень быстро.
Вам нужно быстро и качественно нарезать металл? Воспользуйтесь плазменной резкой! Как правильно ее выполнять, читайте в этой статье.
Если вас интересует, как сделать токарную обработку металлических изделий, читайте статью по https://elsvarkin.ru/obrabotka-metalla/tokarnaya-obrabotka-metalla-obshhie-svedeniya/ ссылке.
Процесс отпуска
Отпуску подвергаются все закаленные детали. Это делается для снятия внутренних напряжений. В результате отпуска несколько снижается твердость и повышается пластичность стали.
В зависимости от требуемой температуры отпуск производится :
- в масляных ваннах;
- в селитровых ваннах;
- в печах с принудительной воздушной циркуляцией;
- в ваннах с расплавленной щелочью.
Температура отпуска зависит от марки стали и требуемой твердости изделия, например, инструмент, для которого необходима твердость HRC 59 – 60, следует отпускать при температуре 150 – 200 градусов. В этом случае внутренние напряжения уменьшаются, а твердость снижается незначительно.
Быстрорежущая сталь отпускается при температуре 540 – 580 градусов. Такой отпуск называют вторичным отвердением, так как в результате твердость изделия повышается.
Изделия можно отпускать на цвет побежалости, нагревая их на электроплитах, в печах, даже в горячем песке. Окисная пленка, которая появляется в результате нагрева, приобретает различные цвета побежалости, зависящие от температуры. Прежде чем приступать к отпуску на один из цветов побежалости, надо очистить поверхность изделия от окалины, нагара масла и т. д.
Обычно после отпуска металл охлаждают на воздухе. Но хромоникелевые стали следует охлаждать в воде или масле, так как медленное охлаждение этих марок приводит к отпускной хрупкости.
Закалка. Это процесс термической обработки, при которой сталь нагревают до оптимальной температуры, выдерживают при этой температуре и затем быстро охлаждают с целью получения неравновесной структуры. В результате закалки повышается прочность и твердость и понижается пластичность конструкционных и инструментальных сталей и сплавов. Качество закалки зависит от температуры и скорости нагрева, времени выдержки и охлаждения. Основными параметрами закалки являются температура нагрева и скорость охлаждения.
Температуру нагрева для закалки определяют по положению критических точек Ac1 и Ас3. Доэвтектоидные углеродистые стали при закалке нагревают на 30-50°С выше верхней критической точки Ас3, а заэвтектоидные - на 30-50°С выше точки Ас1 (рис. 41).
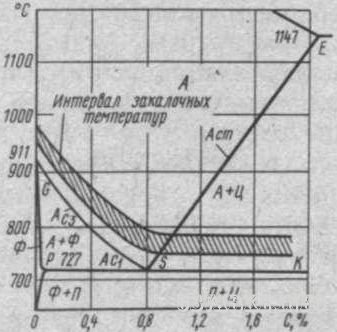
Рис. 41. Интервалы температур нагрева стали при закалке
Скорость нагрева и время выдержки зависят от химического состава стали, размеров, массы и конфигурации закаливаемых деталей, типа нагревательных печей и нагревательной среды. Чем больше размеры и сложнее конфигурация закаливаемых деталей, тем медленнее происходит нагрев. Детали из высокоуглеродистых и легированных сталей, имеющих пониженную теплопроводность, нагревают медленно и с более длительной выдержкой при нагреве по сравнению с деталями из низкоуглеродистых сталей. Это делается для того, чтобы уменьшить деформацию деталей при нагреве.
Скорость нагрева и продолжительность выдержки определяют экспериментально или по технологическим картам, в которых указывают температуру, время нагрева для каждого вида деталей или инструмента. Ориентировочно время нагрева в электрических печах принимают 1,5-2 мин на 1 мм сечения изделия.
Оборудованием для нагрева стали служат нагревательные термические печи и печи-ванны, которые подразделяют на электрические и топливные, обогреваемые за счет сгорания топлива (газа, мазута, угля и др.).
Средой, в которой нагревают сталь, являются в печах - газовая среда (воздух, продукты сгорания топлива), нейтральный газ; в печах-ваннах - минеральные масла, расплавленные соли и металлы.
При нагреве в электрических печах в среде атмосферного воздуха, а также в печах с газовой средой сталь, взаимодействуя со средой, окисляется и на ее поверхности образуется окалина. Кроме того, происходит обезуглероживание - частичное выгорание углерода в поверхностных слоях стали, что снижает прочностные свойства материала после закалки. Наиболее благоприятен нагрев в печах с нейтральной или защитной атмосферой, обеспечивающей предохранение деталей от окисления.
Нагрев стали до требуемой температуры и выдерживание при этой температуре необходимо проводить как можно быстрее. Чем меньше сталь будет находиться в условиях высоких температур, тем выше ее свойства после закалки. Однако время нагрева должно быть достаточным, чтобы сталь равномерно прогревалась по всему объему и получила аустенитную структуру. Поэтому наиболее эффективным по скорости нагрева и предупреждению окисления стали является нагрев в печах-ваннах, наполненных расплавленным металлом (свинец) или расплавленными солями: NaOH, ВаСl2 или 50% КСl+50% NaC03. Нагрев в печах-ваннах с использованием расплавленного металла или солей происходит в 4-5 раз быстрее, чем в печах с газовой средой.
В качестве закалочных сред используют воду, водные растворы солей, щелочей, масло и расплавленные соли, имеющие различную охлаждающую способность. Если принять охлаждающую способность воды при 20°С за единицу, то охлаждающая способность масла будет равна 0,17-0,44, расплавленного свинца (при 335°С) - 0,05, воздуха - 0,03. При нагреве воды с 20 до 99°С охлаждающая способность ее изменяется от 1 до 0,07. В зоне перлитных превращений (650°С) вода охлаждает в 5-6 раз быстрее, чем масло. Воду применяют в основном для охлаждения углеродистых сталей. В масле охлаждают легированные стали.
Закалочные среды (вода, масло) действуют следующим образом. На первом этапе, в момент погружения изделия в закалочную среду, вокруг изделия образуется пленка перегретого пара (паровая рубашка). Через слой паровой рубашки охлаждение изделия происходит относительно медленно. Это этап пленочного кипения. Затем паровая рубашка разрывается и охлаждающая жидкость начинает кипеть на поверхности изделия. Это этап пузырчатого кипения. На этом втором этапе охлаждение изделия происходит быстро. Когда температура поверхности изделия станет ниже температуры кипения жидкости, жидкость не кипит и охлаждение изделия замедлится. Это третий этап - этап конвективного теплообмена. Чем шире интервал этапа пузырчатого кипения, тем интенсивнее охлаждает сталь закалочная жидкость.
Закалка в одной среде – наиболее простой и распространенный способ (рис. 42, кривая а). Деталь или инструмент, нагретые до температуры закалки, погружают в закалочную жидкость (вода, масло и т. д.), в которой она находится до полного охлаждения.
Этот способ используют при ручной и механизированной закалке, когда детали автоматически поступают из печи после нагрева в закалочную жидкость, в воду или масло. Недостатком этого способа закалки является то. что деталь охлаждается по сечению неравномерно и в ней возникают большие термические напряжения.
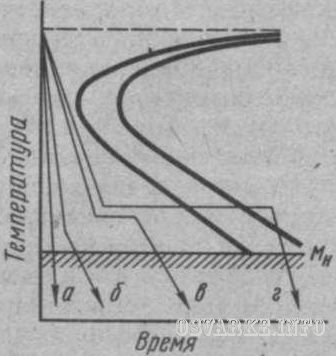
Рис. 42. Схема различных способов закалки:
а - закалка в одной среде, б - закалка в двух средах, в - ступенчатая закалка, г - изотермическая закалка
При закалке в двух средах, или прерывистой закалке (рис. 42, кривая б), деталь, нагретую до заданной температуры, сначала погружают в быстро охлаждающую среду - воду, а затем переносят деталь в медленно охлаждающую среду - масло. Такую закалку применяют для обработки инструмента, изготовленного из высокоуглеродистой стали. При этом способе закалки трудно определить точное время пребывания детали в каждой из сред.
Ступенчатая закалка (рис. 42, кривая в) заключается в том, что нагретые детали сначала охлаждают до температуры несколько выше мартенситной точки Мн в горячем масле или расплавленной соли, а затем после короткой изотермической выдержки, необходимой для выравнивания температуры по всему сечению изделия, охлаждают на воздухе. Длительность изотермической выдержки по времени должна быть меньше времени устойчивости аустенита при этой температуре. На второй стадии охлаждения сталь закаливается. При таком виде закалки уменьшаются термические напряжения, коробление и предотвращается образование трещин.
Изотермическая закалка (рис. 42, кривая г) выполняется так же, как и ступенчатая, но выдержка в закалочной среде более продолжительная. При такой выдержке происходит изотермический распад аустенита с образованием бейнита. В качестве закалочной среды используют расплавленные соли или щелочи (20% NaOH и 80% КОН) с добавками 5-10% воды для увеличения скорости охлаждения. Изотермической закалке подвергают детали и инструмент из легированных сталей марок 6ХС, 9ХС, ХВГ и др.
Закалку с подстуживанием применяют для уменьшения разницы в температурах металла и закалочной среды, если деталь нагрета до температуры, значительно превышающей температуру закалки данной стали. Нагретую деталь перед погружением в закалочную среду выдерживают (подстуживают) на спокойном воздухе. Этот способ закалки обеспечивает уменьшение внутренних напряжений и предотвращает коробление деталей, особенно деталей, подвергнутых цементации
Закалка с самоотпуском состоит в том, что нагретую деталь . рабочей частью погружают в закалочную среду и выдерживают в ней не до полного охлаждения. За счет тепла нерабочей части детали, которая не погружалась в закалочную жидкость, рабочая часть детали или инструмента нагревается. Температуру отпуска при этом способе закалки определяют по цветам побежалости, возникающим на поверхности детали при температурах 220-300°С.
Закалку с самоотпуском применяют для обработки зубил, кернеров, бородков и других ударных инструментов, у которых твердость должна плавно понижаться от рабочей части к нерабочей.
Закалка с обработкой холодом заключается в продолжении охлаждения закаленной стали до температур ниже комнатной, но в интервале начала (Мн) и окончания (Мк) мартенситного превращения (см. рис. 38), для дополнительного более полного превращения остаточного аустенита в мартенсит и повышения твердости. Высокоуглеродистые и легированные стали после закалки при комнатной температуре содержат до 12% остаточного аустенита, а быстрорежущие - более.35%. В результате обработки холодом повышается твердость и стабилизируются размеры деталей. Наиболее распространенной охлаждающей средой служит смесь ацетона и твердой углекислоты (-78°С).
Закаливаемость - это способность стали приобретать максимально высокую твердость после закалки. Закаливаемость зависит главным образом от содержания углерода в стали: чем больше углерода, тем выше твердость. Это объясняется тем, что с повышением содержания углерода увеличивается число атомов углерода, удерживаемых в атомной решетке железа при закалке, т. е. увеличивается степень пересыщения твердого раствора углерода в железе.
Углеродистые стали с содержанием углерода менее 0,3% (сталь 20, СтЗ) не способны принимать закалку, так как не происходит образования мартенситной структуры. Образование мартенситной структуры связано с перестройкой атомной решетки железа из гранецентрированной в объемно-центрированную. Температура, при которой происходит такая перестройка, зависит от содержания углерода (см. рис. 38). Чем больше содержание углерода, тем ниже температура образования мартенситной структуры.
При выборе охлаждающей среды для того или иного способа закалки необходимо учитывать закаливаемость и прокаливаемость данной стали.
Прокаливаемость - это глубина проникновения закаленной зоны, т. е. способность стали закаливаться на определенную глубину. За глубину закаленной зоны принимают расстояние от поверхности до слоя, где в структуре будет примерно одинаковое количество мартенсита и троостита. Прокаливаемость зависит от химического состава стали, размеров деталей и условий охлаждения. С увеличением содержания углерода до 0,8% прокаливаемость стали увеличивается. При дальнейшем увеличении углерода прокаливаемость несколько снижается. Увеличению прокаливаемости также способствует укрупнение зерен аустенита при нагреве под закалку. Нерастворимые частицы, неоднородность аустенита и другие факторы, которые уменьшают устойчивость переохлажденного аустенита, уменьшают прокаливаемость. Все легирующие элементы, за исключением кобальта, увеличивают прокаливаемость. При комплексном легировании полезное влияние отдельных элементов на прокаливаемость взаимно усиливается.
При закалке скорость охлаждения по сечению изделия распределяется неравномерно. У поверхности она максимальная, в центре - минимальная, т. е. скорость охлаждения уменьшается по некоторому закону от поверхности изделия к его центру. Характеристикой прокаливаемости является критический диаметр, т. е. диаметр максимального сечения, которое прокаливается полностью в данной охлаждающей среде.
Отпуск - процесс термической обработки, состоящий в нагреве закаленной стали до температуры ниже критической точки Ас1), выдержке при этой температуре и последующем охлаждении (обычно на воздухе). Цель отпуска - получение более устойчивого структурного состояния, устранение или уменьшение напряжений, повышение вязкости и пластичности, а также понижение твердости и уменьшение хрупкости закаленной стали (рис. 43). Правильное выполнение отпуска в значительной степени определяет качество закаленной детали. Температура отпуска варьируется в широких пределах - от 150 до 700°С в зависимости от его цели. Различают низкий, средний и высокий отпуск.
Низкий отпуск характеризуется нагревом в интервале 150-250°С, выдержкой при этой температуре и последующим охлаждением на воздухе. Он выполняется с целью получения структуры мартенсита отпуска и для частичного снятия внутренних напряжений в закаленной стали с целью повышения вязкости без заметного снижения твердости. Низкий отпуск применяют для инструментальных сталей, после цементации и т. д.
Средний отпуск производится при температурах 300-500°С для получения структуры троостита отпуска. Твердость сталей заметно понижается, вязкость увеличивается. Этот отпуск применяют для пружин, рессор, а также инструмента, который должен иметь значительную прочность и упругость при достаточной вязкости.

Рис. 43. Влияние температуры отпуска на механичесуие свойства стали 40
Доставка готовой продукции нашей компании осуществляется 2-мя способами:
- Самовывоз с территории предприятия;
- Доставка до терминала транспортной компании «Деловые Линии». Далее продукция до покупателя доставляется через ТК «Деловые Линии».
Отпуск – вид термической обработки, в результате которой существенно повышается пластичность металлической заготовки, а также снижается ее хрупкость. Для того чтобы отпуск был произведен в соответствии с нормами технического регламента, следует использовать профильные, надежные печи, способные обеспечить поддержание необходимой температуры на протяжении всего процесса обработки.
Печи для отпуска металлов от производителя
Производственная компания «Сикрон» осуществляет выпуск печей для отпуска самой различной конфигурации. В ассортименте решения для небольших предприятий, а также габаритные установки, ориентированные на крупные производственные организации.
При изготовлении продукции используются качественные, стойкие к износу материалы, а также надежные комплектующие. Сборка оборудования осуществляется в соответствии с требованиями отраслевых стандартов. Печи в полной мере адаптированы к работе в жестких производственных условиях.
Каждая промышленная печь для отпуска, выпускаемая компанией «Сикрон», комплектуется полным набором сопроводительных документов (паспорта, сертификаты и тд.), на все оборудование распространяется гарантия завода-изготовителя.
Клиентами завода может быть приобретена печь шахтная для отпуска либо камерная установка. Продукция изготавливается как по типовым чертежам, так и по индивидуальным заказам. Во втором случае клиенту требуется предоставить подробное техническое задание, содержащее сведения относительно специфики подготавливаемого оборудования (габариты рабочей камеры, особенности системы управления и тд.). Для подачи заявки достаточно связаться с представителями завода посредством телефона либо электронной почты.
Обращаем Ваше внимание, что в таблицах указаны самые популярные параметры печей. Мы также можем изготовить для Вас печь с нестандартными размерами и характеристиками.
Печи для отпуска металлов | ||||||||||||
№, п/п | Рабочее пространство, ШхГхВ, мм | Обьем, л | t раб., °С | P, кВт | Цена | |||||||
1 | 400 х 800 х 400 | 128 | 700 | 21 | Расчет стоимости | |||||||
2 | 500 х 800 х 500 | 200 | 700 | 27 | Расчет стоимости | |||||||
3 | 600 х 800 х 400 | 192 | 700 | 30 | Расчет стоимости | |||||||
4 | 600 х 800 х 600 | 288 | 700 | 30 | Расчет стоимости | |||||||
5 | 600 х 1200 х 500 | 360 | 700 | 30 | Расчет стоимости | |||||||
6 | 600 х 1200 х 600 | 432 | 700 | 36 | Расчет стоимости | |||||||
7 | 800 х 1200 х 500 | 480 | 700 | 42 | Расчет стоимости | |||||||
8 | 800 х 1600 х 800 | 1024 | 700 | 70 | Расчет стоимости | |||||||
9 | 1000 х 2000 х 1000 | 2000 | 700 | 90 | Расчет стоимости |
Печи для отпуска металлов с выкатным подом | ||||||||||||
№, п/п | Рабочее пространство, ШхГхВ, мм | Обьем, л | t раб., °С | P, кВт | Цена | |||||||
1 | 600х1000х500 | 300 | 700 | 30 | Расчет стоимости | |||||||
2 | 800х1000х600 | 480 | 700 | 42 | Расчет стоимости | |||||||
3 | 800х1600х800 | 1024 | 700 | 60 | Расчет стоимости | |||||||
4 | 1000х2000х1000 | 2000 | 700 | 90 | Расчет стоимости | |||||||
5 | 1000х3000х1000 | 3000 | 700 | 120 | Расчет стоимости | |||||||
6 | 1000х6000х1000 | 6000 | 700 | 240 | Расчет стоимости | |||||||
7 | 1500х1500х1000 | 2250 | 700 | 90 | Расчет стоимости | |||||||
8 | 1500х1500х1500 | 3375 | 700 | 120 | Расчет стоимости | |||||||
9 | 1500х2000х1000 | 3000 | 700 | 120 | Расчет стоимости | |||||||
10 | 1500х2000х1500 | 4500 | 700 | 180 | Расчет стоимости | |||||||
11 | 1500х3000х1000 | 4500 | 700 | 180 | Расчет стоимости | |||||||
12 | 1500х3000х1500 | 6750 | 700 | 210 | Расчет стоимости | |||||||
13 | 2000х2000х1000 | 4000 | 700 | 180 | Расчет стоимости | |||||||
14 | 2000х3000х1500 | 9000 | 700 | 240 | Расчет стоимости | |||||||
15 | 2000х3000х2000 | 12000 | 700 | 330 | Расчет стоимости | |||||||
16 | 2000х4000х2000 | 16000 | 700 | 600 | Расчет стоимости | |||||||
17 | 2000х5000х2000 | 20000 | 700 | 800 | Расчет стоимости | |||||||
18 | 2000х7000х2000 | 28000 | 700 | 1100 | Расчет стоимости |
Технология и виды отпуска материалов
Обработка заготовки в печи для отпуска с целью снятия остаточных напряжений, уменьшения хрупкости производится посредством нагрева закаленных деталей до температуры ниже критической. Такой метод позволяет получить различные состояния материала, которые отличаются по структуре и свойствам от исходной заготовки.
Печи для отпуска позволяют использовать следующие технологии обработки в зависимости от теплового режима:
- низкий отпуск. Заготовка нагревается до 200–300°С, что вызывает уменьшение твердости и увеличение пластических характеристик материала. За счет этого удаляются внутренние напряжения в изделиях;
- средний отпуск - деталь нагревается до 300–500°С. Чем выше нагрев, тем большую пластичность и вязкость приобретает материал;
- высокий отпуск при температурах 500–700°С повышает механические свойства материала, такие как прочность, пластичность и вязкость. Поэтому эта технология применяется для термообработки пружин, рессор, автомобильных осей и прочих деталей, которые подвержены действию высоких напряжений.
В нашей компании Вы можете купить печи для отпуска без наценок и переплат. Мы предлагаем услуги доставки заказа по России, странам СНГ и таможенного союза.
Оборудование используют в металлургической промышленности. Закалка – вид термической обработки стали, после которого материал наделяется высокими показателями прочности и надежности. Печь для закалки бывает разных типов:
- камерной;
- шахтной;
- туннельной;
- элеваторной.
Также существуют печи для закалки стали колпаковые и барабанные. Самыми востребованными считаются первые четыре вида.
Камерная печь для закалки металла представляет собой не слишком массивную конструкцию. Она состоит из следующих элементов:
- корпуса, защищенного специальным кожухом;
- рабочей камеры с нагревательными элементами;
- смотрового окна для визуализации техпроцесса;
- дверки для выгрузки и загрузки изделий.
Муфельная печь для закалки металла цена на которую низкая у производителя, позволяет равномерно прогревать все материалы, находящиеся в рабочем пространстве. С помощью специальных приспособлений есть возможность регулировать температурный режим. Стоит учесть, что камерная печь для закалки металла (цена оптимальная у официального дистрибьютора) характеризуется малым потреблением электрической энергии. Ее корпус выполнен из прочных и жароустойчивых материалов.
Термическая печь для закалки металла оснащается нагревательными элементами, которые выполнены из кремния, фехрали, карбито-кремния, проволоки и нихрома. Благодаря этой конструктивной особенности агрегаты имеют длительный срок эксплуатации.
Проходные печи для закалки относят к категории камерного и туннельного оборудования. Они оснащаются такими рабочими элементами:
- камерой для закалки (рабочая температура до +950 градусов);
- камерой для отпуска (рабочая температура до +700 градусов);
- закалочной ванной, которая заполняется водой, маслом (вакуумная печь для закалки в масло) или полимером (зависит от обрабатываемого вида стали);
- холодильным агрегатом;
- установкой для полоскания и обезжиривания;
- холодильной камерой;
- приспособлением для поворота камеры;
- роликовыми установками для загрузки и выгрузки изделий.
Печь для закалки металла (цена зависит от комплектации оборудования) оснащена устройствами для автоматизированного управления технологическим процессом. Это позволяет значительно сократить физические затраты на обслуживание оборудования.
К такой категории агрегатов относятся конвейерные печи для закалки саморезов. Они имеют различный размер и комплектацию. Есть установки, которые эффективно используют в малом бизнесе. Для предприятий крупных масштабов подойдут агрегаты с большей мощностью и размером рабочего пространства.
Если потребуется вакуумная камерная печь для закалки, купить ее можно в специализированном магазине. При выборе оборудования стоит обратить внимание на его мощность и объем рабочего пространства.
Особой популярностью пользуется печь для закалки металла СНОЛ. Также ее можно использовать для закалки фарфора, керамики и стекла. Агрегат оснащен выдвижным подом. Во время технологического процесса можно догружать дополнительно изделия для обработки.
Печь шахтная для закалки не менее востребована, чем предыдущая установка. С ее помощью производится закалка изделий, имеющих значительную длину. Одним из видов оборудования является печь для закалки гриф штанги. Изделия, которые прошли такую обработку наделяются жесткостью, прочностью и устойчивостью к истиранию.
Шахтная вакуумная печь для закалки деталей имеет цилиндрическую форму. В рабочем пространстве, которое разделяется на определенные вертикальные зоны, размещают обрабатываемые изделия. Первая область находится в самом низу. Вторая – чуть выше. В ней выполняется подогрев материала. Третья зона – охлаждающая. В нее поступает холодный воздух. После завершения процесса эта зона начинает нагреваться до +500 градусов.
Купить печь для закалки металла довольно просто. Для этого необходимо посетить специализированный магазин. При выборе оборудования стоит обратить внимание на футеровку. Шахтная печь для закалки (цена установлена производителем) должна быть футерована шамотным кирпичом. Этот материал отлично держит тепло. Некоторые виды агрегатов футеруют простыми теплоизоляционными средствами: минеральной ватой и подобными. Они не предназначены для работы с большими объемами.
Туннельные агрегаты могут быть такими: термические печи для закалки и те, которые работают на твердом топливе или газе. По принципу своей конструкции они напоминают камерные установки проходного типа.
Туннельная вакуумная печь для закалки пружин и других металлических деталей представляет собой установку, выполненную в форме туннеля – рабочее пространство. В нем происходит закалка материала. Изделия с помощью вагонеток и рельс передвигаются по туннелю навстречу продуктам горения.
Можно также купить печь для закалки металлических изделий элеваторного типа. Такой агрегат характеризуется минимальным показателем теплопотери. Его размеры незначительные, что дает возможность устанавливать оборудование в небольших цехах.
Колпаковая печь не менее популярна в металлургической промышленности. С ее помощью выполняют закалку металлических деталей к авиационной технике.
Она наделена такими преимуществами:
- незначительным удельным весом теплопокрытия (футеровка);
- высокий показатель эффективности;
- надежностью;
- прочностью – корпус агрегата выполнен из высокопрочной стали;
- простотой эксплуатации и облуживания.
Купить муфельную печь для закалки металла или другой вид оборудования не составит труда. Изначально необходимо точно просчитать объемы производства, а также требуемую мощность агрегата.
Вакуумные печи закалки
Оборудование нашло широкое применение в металлургии. С его помощью не только закаляют изделия, но и выполняют ковку. Печь для закалки камерного типа может использоваться как в крупных масштабах производства, так и в небольших.
Закалка стали в вакуумных печах имеет ряд преимуществ. Металлические изделия наделяются такими свойствами:
- прочностью;
- стойкостью на излом;
- надежностью;
- износостойкостью;
- устойчивостью к истиранию.
Металл становится плотнее, что дает возможность ему выдерживать разнообразные механические и физические воздействия. В вакуумных печах можно не только закалять металлические изделия, но различные строительные материалы.
Металлоизделия, используемые в любых отраслях хозяйства должны отвечать требованиям устойчивости к износу. Для этого используется воздействие высокими температурами, в результате чего усиливаются нужные эксплуатационные свойства. Этот процесс называется термической обработкой.
Термообработка представляет собой комплекс операций нагрева, охлаждения и выдержки металлических твердых сплавов для получения необходимых свойств благодаря изменению структуры и внутреннего строения. Термическая обработка применяется в качестве промежуточной операции для того, чтобы улучшить обрабатываемость резанием, давлением, либо в качестве окончательной операции технологического процесса, которая обеспечивает требуемый уровень свойств детали.
Различные методы закаливания применялись с давних пор: мастера погружали нагретую металлическую полоску в вино, в масло, в воду. Для охлаждения кузнецы порой применяли и достаточно интересные способы, например садились на коня и мчались, охлаждая изделие в воздухе.
По способу совершения термическая обработка бывает следующих видов:
-Термическая (нормализация, закалка, отпуск, отжиг, старение, криогенная обработка).
-Термо-механическая. Включает обработку высокими температурами в сочетании с механическим воздействием на сплав.
-Химико-термическая. Подразумевает термическую обработку металла с последующим обогащением поверхности изделия химическими элементами (углеродом, азотом, хромом и др.).
Основные вид ы термической обработки:
1. Закалка. Представляет собой вид термической обработки разных материалов (металлы, стекло), состоящий в нагреве их выше критической температуры с быстрым последующим охлаждением. Выполняется для получения неравновесных структур с повышенной скоростью охлаждения. Закалка может быть как с полиморфным превращением, так и без полиморфного превращения.
2. Отпуск – это технологический процесс, суть которого заключается в термической обработке закалённого на мартенсит металла либо сплава, основными процессами при котором являются распад мартенсита, рекристаллизация и полигонизация. Проводится с целью снятия внутренних напряжений, для придания материалу необходимых эксплуатационных и механических свойств.
3. Нормализация. В данном случае изделие нагревается до аустенитного состояния и потом охлажда е т ся на спокойном воздухе. В результате нормализации снижаются внутренние напряжения, выполняется перекристаллизация стали. В сравнении с отжигом, нормализация – процесс более короткий и более производительны й .
4. Отжиг. Представляет собой операцию термической обработки, заключающуюся в нагреве стали, выдержке при данной температуре и последующем медленном охлаждении вместе с печью. В результате отжига образуется устойчивая структура, свободная от остаточных напряжений. Отжиг является одной из важнейших массовых операций термической обработки стали.
1) Снижение твердости и повышение пластичности для облегчения обработки металлов резанием;
2) Уменьшение внутреннего напряжения, возникающего после обработки давлением (ковка, штамповка), механической обработки и т. д.;
3) Снятие хрупкости и повышение сопротивляемости ударной вязкости;
4) Устранение структурной неоднородности состава материала, возникающей при затвердевании отливки в результате ликвации.
Для цветных сплавов (алюминиевые, медные, титановые) также широко применяется термическая обработка. Цветные сплавы подвергают как разупрочняющей, так и упрочняющей термической обработке, в зависимости от необходимых свойств и области применения.
Термическая обработка металлов и сплавов является основным технологическим процессом в чёрной и цветной металлургии. На данный момент в распоряжении технических специалистов множество методов термообработки, позволяющих добиться нужных свойств каждого вида обрабатываемых сплавов. Для каждого металла свойственна своя критическая температура, а это значит, что термообработка должна производиться с учётом структурных и физико-химических особенностей вещества. В конечном итоге это позволит не только достичь нужных результатов, но и в значительной степени рационализировать производственные процессы.
Читайте также:
- Индексируется ли компенсация за неиспользованный отпуск при увольнении
- Как в сзв стаж отразить отпуск без сохранения заработной платы
- Почему декретный отпуск так называется
- Может ли безработная беременная женщина получить декретные
- Можно ли брать отпуск без сохранения заработной платы на несколько часов